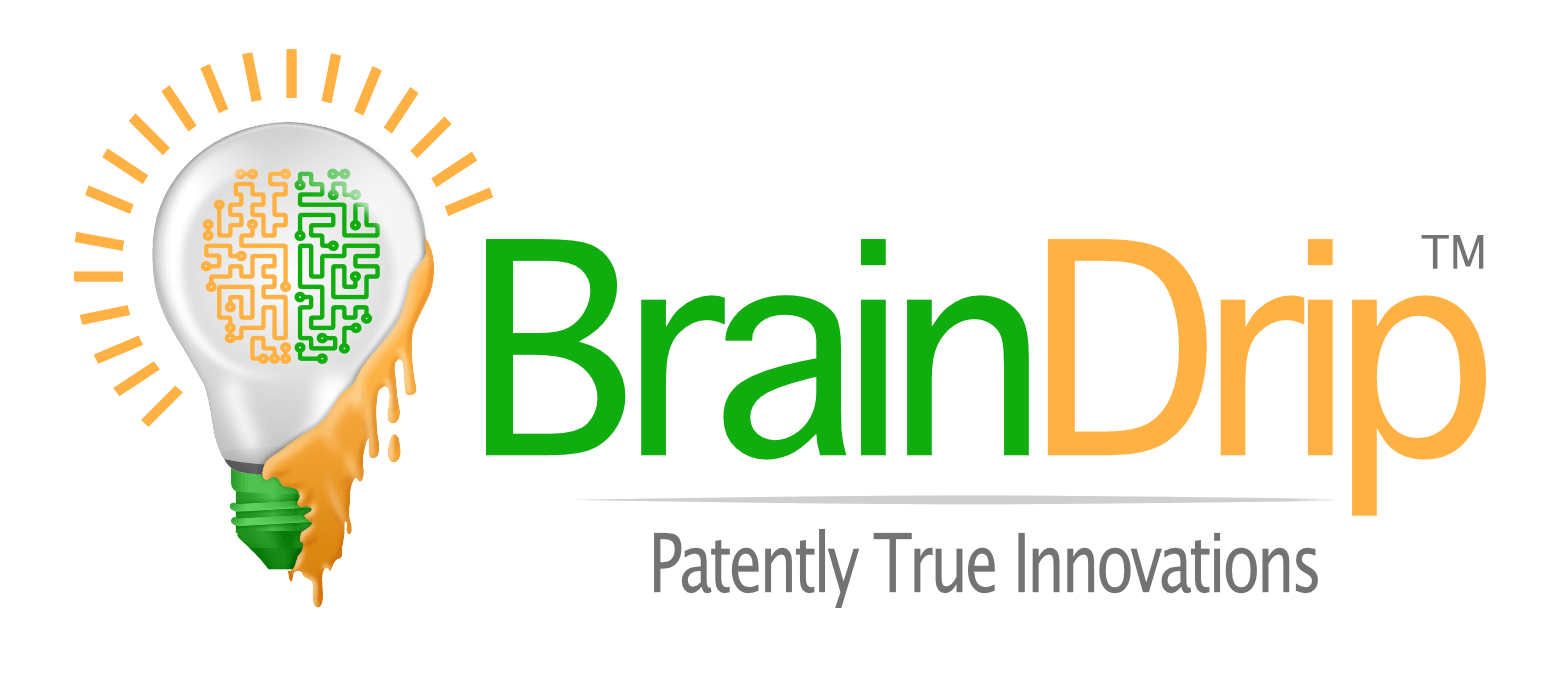
Our Products
Composite Pipeline
Our Products
Composite Pipeline
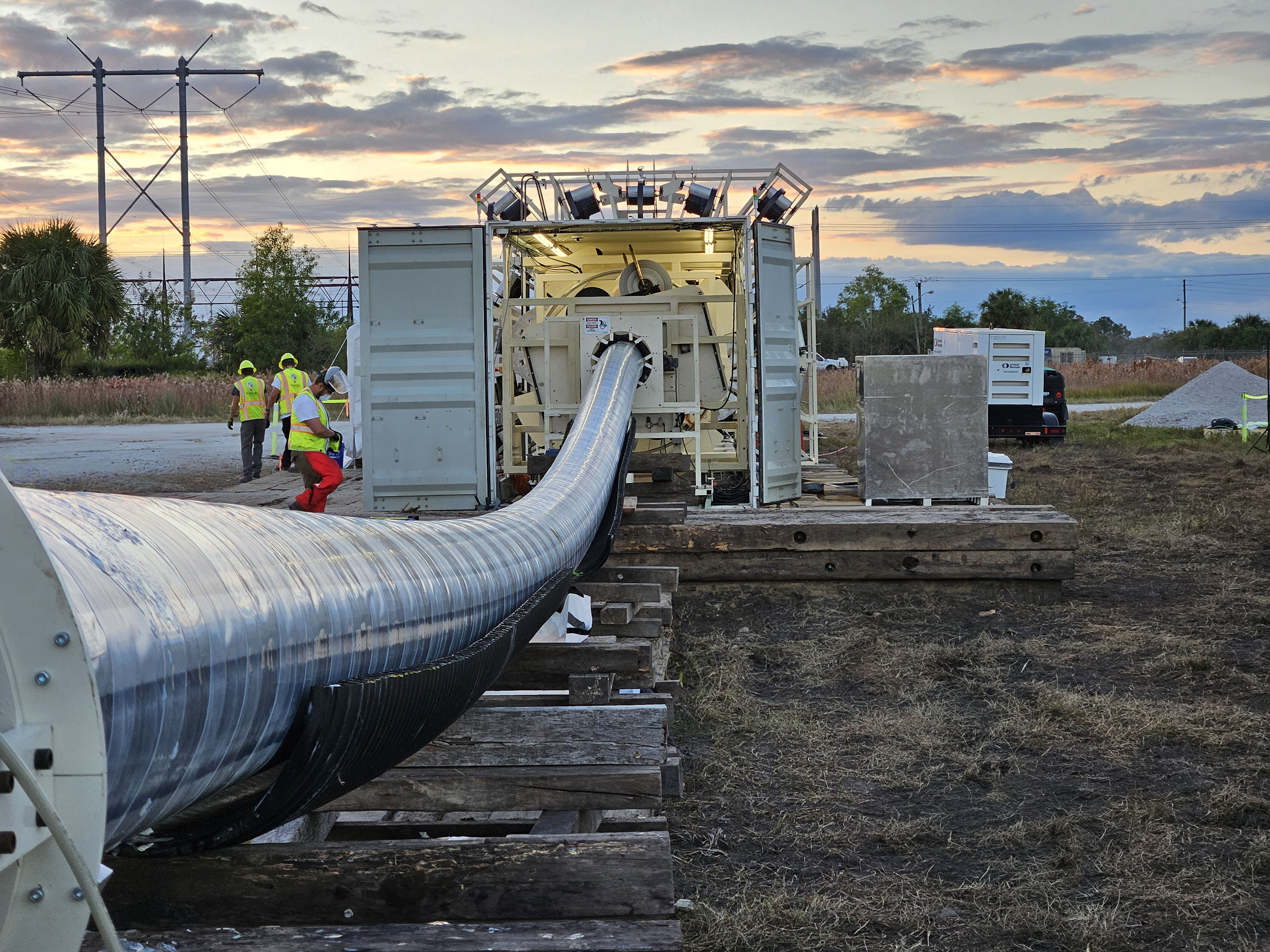
A Modern Solution for Aging Systems
BrainDrip’s composite pipeline product, is a groundbreaking solution designed to address the challenges of aging and outdated pipeline infrastructure. With many pipelines operating well beyond their intended lifespans, the product offers a path forward by combining advanced composite materials with on-site manufacturing capabilities.
Whether you need to rehabilitate existing pipelines or install new greenfield systems, BrainDrip's solution delivers reliability, flexibility, and operational confidence. Its innovative design meets the demands of modern energy markets, offering seamless compatibility with today’s fuels—like natural gas—and tomorrow’s, including hydrogen and CO2.
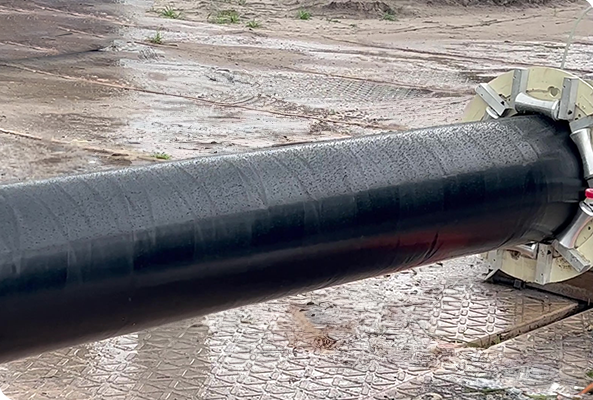
Custom Solutions for Every Project
Flexible Diameters for Varied Applications
Every pipeline project is unique, and the composite pipeline adapts to meet specific design requirements. With diameters ranging from 6 to 36 inches, our solution is tailored for projects across transmission and distribution markets. Whether handling large flows, high pressures, or both, the composite pipeline ensures optimal performance with precision manufacturing and rigorous quality assurance.
Engineered for High Pressure
The composite pipeline is built to handle pressure ratings exceeding 3,500 psig, making it an attractive solution for projects involving low-pressure liquids, high-pressure flammable gases, or anything in between. By customizing composite reinforcement levels, we optimize cost while maintaining safety and reliability, no matter the application.
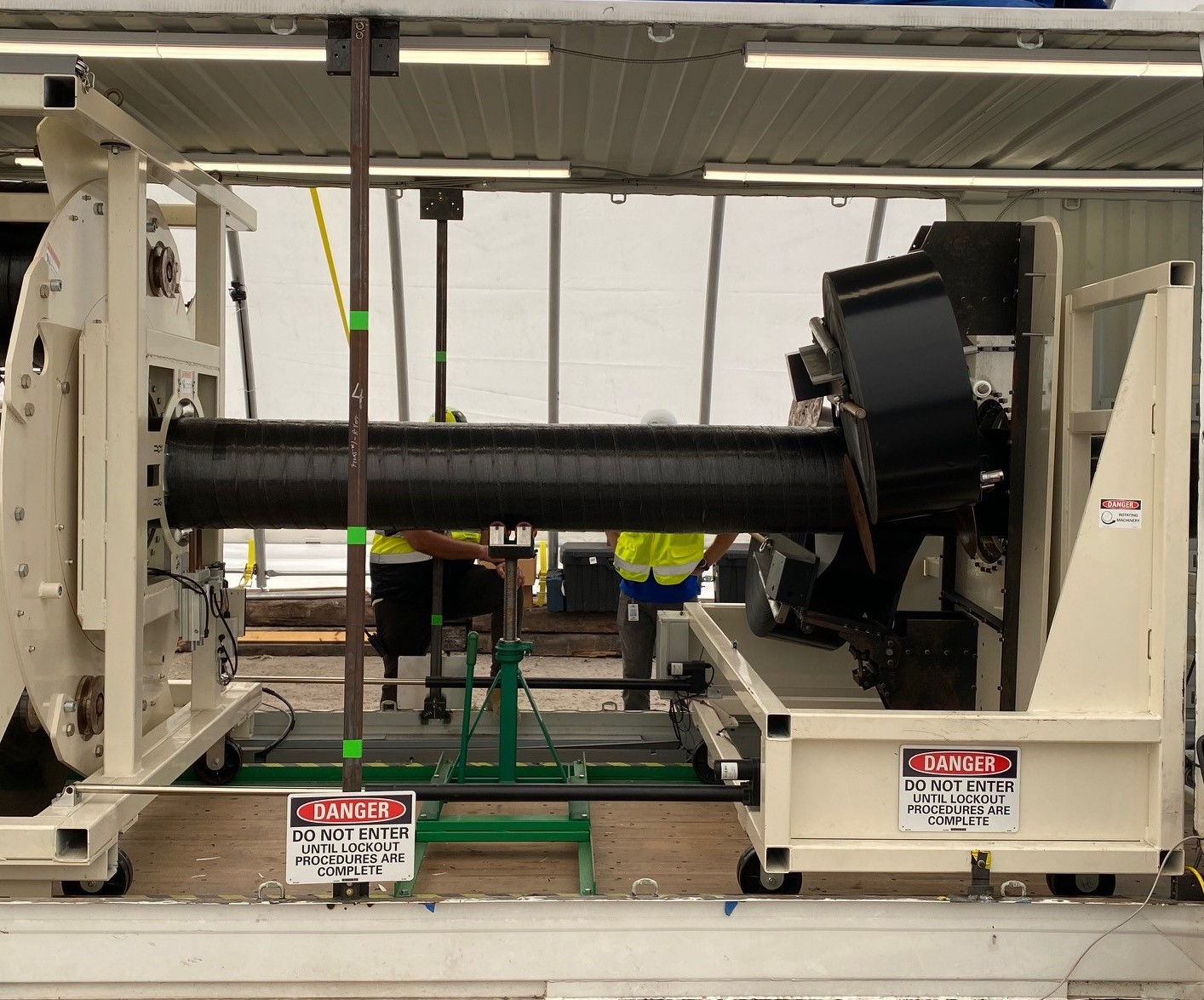
Efficiency Through On-Site Manufacturing
Continuous Lengths for Seamless Performance
With BrainDrip’s field manufacturing, the composite pipeline is manufactured directly at the project site, enabling continuous pipeline lengths of over 10 miles. This eliminates the need for spooled products or excessive jointing, reducing installation time and enhancing operational reliability.
Small Footprint, Big Impact
The compact 53-foot platform allows the composite pipeline to be produced efficiently, even in sensitive environmental areas. Production rates of over one mile per day minimize disruptions and lower project costs, making the composite product an ideal choice for time-sensitive and environmentally conscious projects.
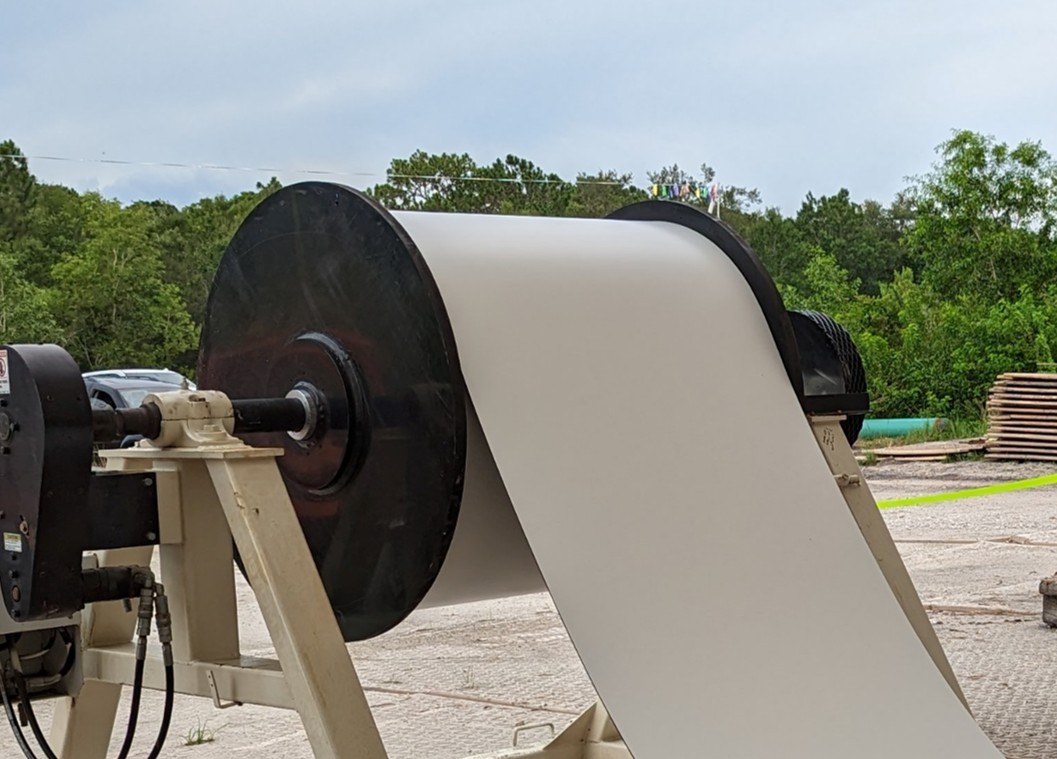
Ready for Changing Markets
Broad Compatibility with Gases and Liquids
Energy markets are evolving rapidly, and the composite pipeline is designed to evolve with them. It offers compatibility with natural gas, hydrogen, CO2, water, NGLs, gasoline, diesel, and more. With features like advanced coextrusions to mitigate permeation, the composite product supports seamless transitions to future energy sources, such as pure hydrogen or natural gas/hydrogen blends.
Future-Proofing Infrastructure
By installing the composite pipeline today, operators ensure that their pipelines are ready for the demands of 2045 and beyond. This future-proof design empowers customers to adapt to market shifts without costly infrastructure overhauls.
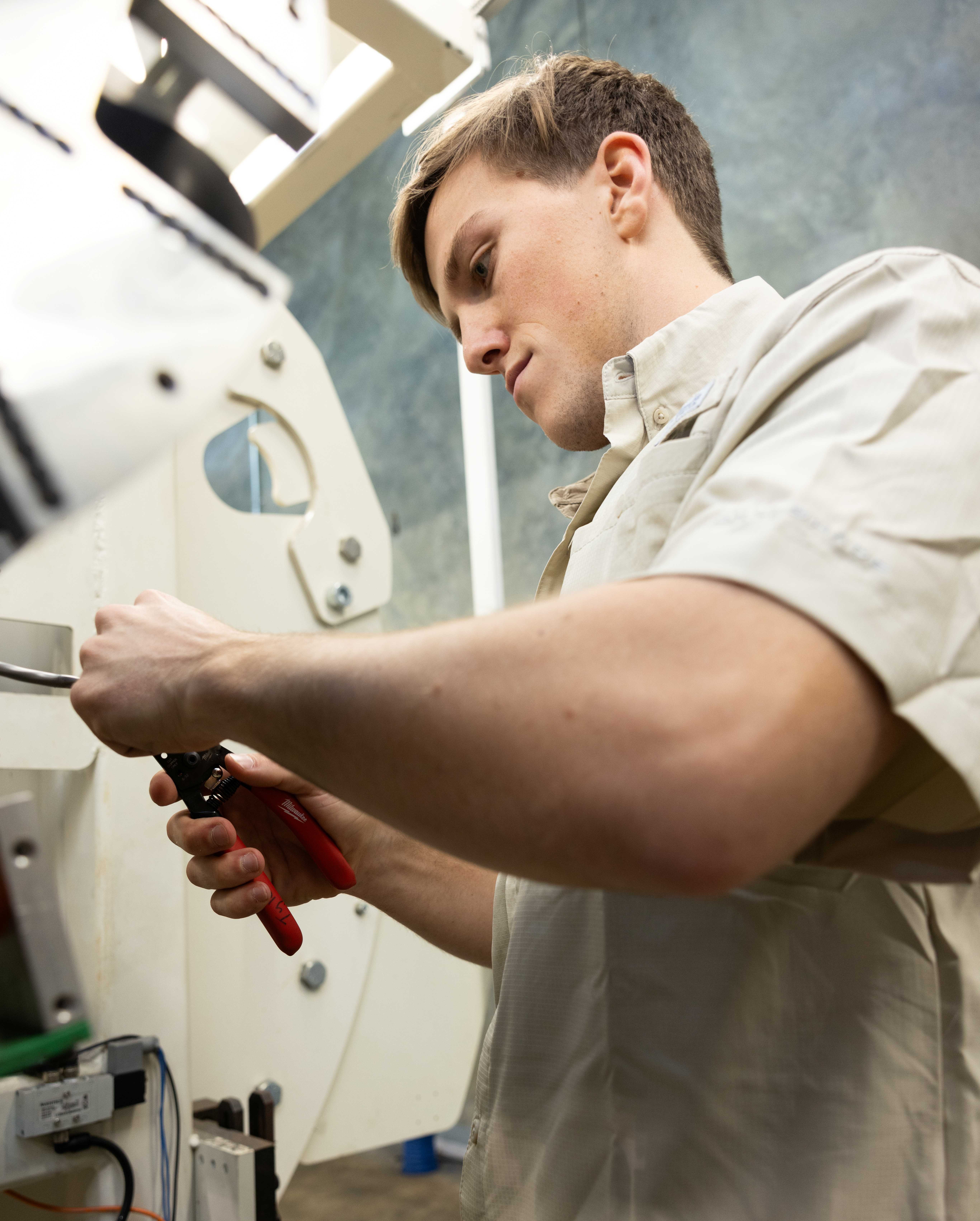
Confidence Through Continuous Monitoring
Integrated Health and Risk Monitoring System
The composite pipeline comes with BrainDrip’s state-of-the-art health monitoring system, delivering real-time monitoring and proactive insights. This system detects third-party threats, environmental disruptions, and potential leaks, ensuring the long-term safety and reliability of your assets. With distributed fiber optic sensing and advanced analytics, the health monitoring system provides:
Detection of encroachment and ground movement
Strain and performance monitoring over the asset's lifetime
Real-time leak detection and localization
Comprehensive performance metrics, including pressure and temperature
This level of monitoring ensures that operators maintain complete control and confidence in their systems, reducing risks and meeting the highest standards of operational safety.

BrainDrip's Composite Pipeline
BrainDrip's Composite Pipeline is more than a pipeline—it’s a transformative solution designed to meet the evolving needs of the energy industry. By combining cutting-edge materials, advanced manufacturing, and integrated monitoring, BrainDrip is redefining how pipelines are built, maintained, and managed.
For a summary of the composite pipeline, a product brochure is available to download here.
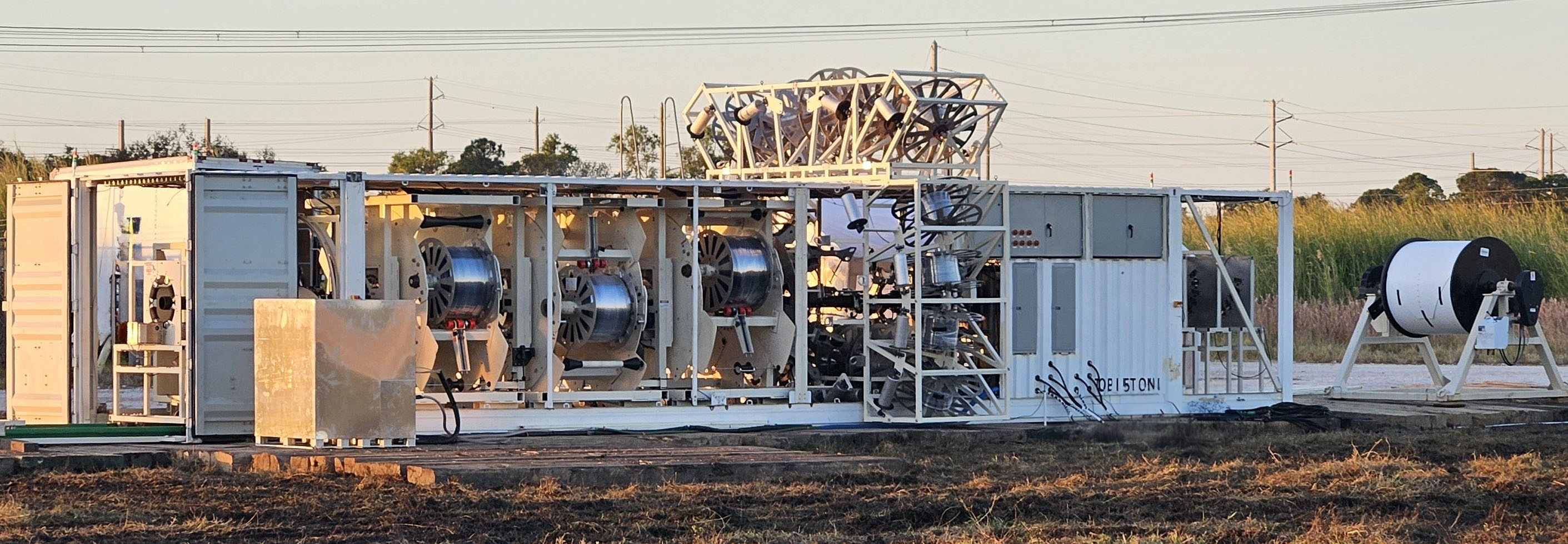
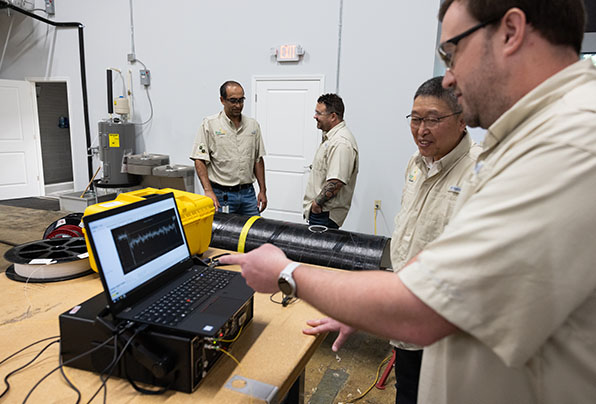
Have a project for us?
Reach out to us to take the next step in getting your project off the ground!
Contact us